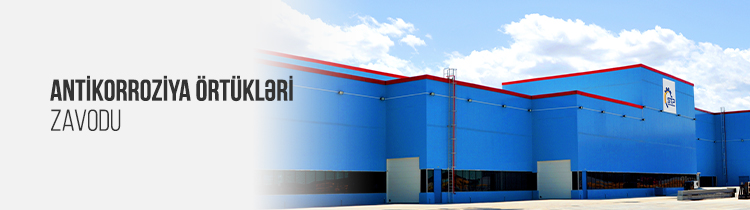
Anticorrosive coatings plant
General information
Applying the experience of Western European countries made it possible to create the most advanced and environmentally friendly anticorrosive coatings production plant in the region.
Applying the experience of Western European countries made it possible to create the most advanced and environmentally friendly anticorrosive coatings production plant in the region. This enterprise has a large production capacity. Currently, the factory runs hot-dip galvanizing, cleaning and painting workshops.
The hot-dip galvanizing shop houses equipment by the German companies Pilling, SCHEFFER and Stoeckl, Austrian companies KOERNER and SCHEUCH and Norwegian company C.H.Evensen. The plant has an annual production capacity of 20,000 tons. Metal constructions with dimensions up to 14,5x1,4x2,7 meters can be galvanized in automatic mode here. Structures of length up to 18 meters can also galvanized in the manual mode.
The quality control of zinc coating is carried out by test methods as per GOST 9.307-89. The metallic composition of the zinc bath is analyzed using a stationary BELEC LAB 3000s spectrometer. Galvanized materials have a service life of up to 75-100 years. They are widely used in areas requiring reliability and durability.
The hot-dip galvanizing process involves lowering metal structures into a molten zinc bath (~ 450-452 ° C). Galvanized materials comply with the requirements of the EN ISO 1461: 2009 and ASTM A123 standards. High-quality (99.995%) zinc is used to ensure high quality work in the galvanizing process.
Depending on the customer's requirements, the cleaning and coloring shop carries out anticorrosive and painting works on various complex metal structures and their parts used in construction, machine building and other industries. The workshop consists of two zones: sandblasting (surface preparation) and painting.
In the sandblasting zone, corrosion, oil and other contaminants are cleaned from the metal surface as per SA 2 and SA 2.5 standards. If this process is not performed before painting, the lifetime of the metal structure is diminished. A well-prepared surface ensures a 10-year + service life for a typical multilayer color system. However, if the same system is applied on a surface containing traces of even the slightest pollution, the service life is diminished to only 4-6 years, and sometimes less. The sandblasting process is carried out using metal crumbs, dry sand, water, flame, steam, manually or by means of mechanical devices.
In the painting zone, materials are painted using traditional and modern technologies.