Hot Galvanizing
The equipment of German company "PILLING", "SCHEFFER", "STOECKL", Austrian company "KOERNER", "SCHEUCH" and Norwegian company "C.H.EVENSEN" has been installed in the hot galvanizing shop with annual production capacity of 20000 tons. Here, in the automatic mode, metal structures with the dimensions up to 14.5x1.4x2.7 meters, and in the manual mode up to 18 meters can be galvanized.
The initial processing of metal combines 9 (nine) units of technological baths locating in compacted area, 3 (three) spreader-bars, the dryer performing simultaneously dry and a scrubber designed to catch the air containing HCl (chloride acid vapor) in the area where the baths are located.
The quality control of zinc coating is carried out by test methods as per GOST 9.307-89. The metallic composition of the zinc bath is analyzed using a stationary BELEC LAB 3000s spectrometer. Galvanized materials have a service life of up to 75-100 years. They are widely used in areas requiring reliability and durability.
Flux layer acts as the catalyst in the galvanizing process. This layer also prevents oxidizations that may occur in drying chambers and during transport of spreader-bars to the zinc bath. The drying process is carried out through heater and under heating conditions up to 110-120 °C.
The hot galvanizing process involves entering metal structures into a molten zinc bath (~450-452 °C). Galvanized materials comply with the requirements of the EN ISO 1461: 2009 and ASTM A123 standards. High quality (99.995 %) zinc is used for providing of high class work in galvanizing process.
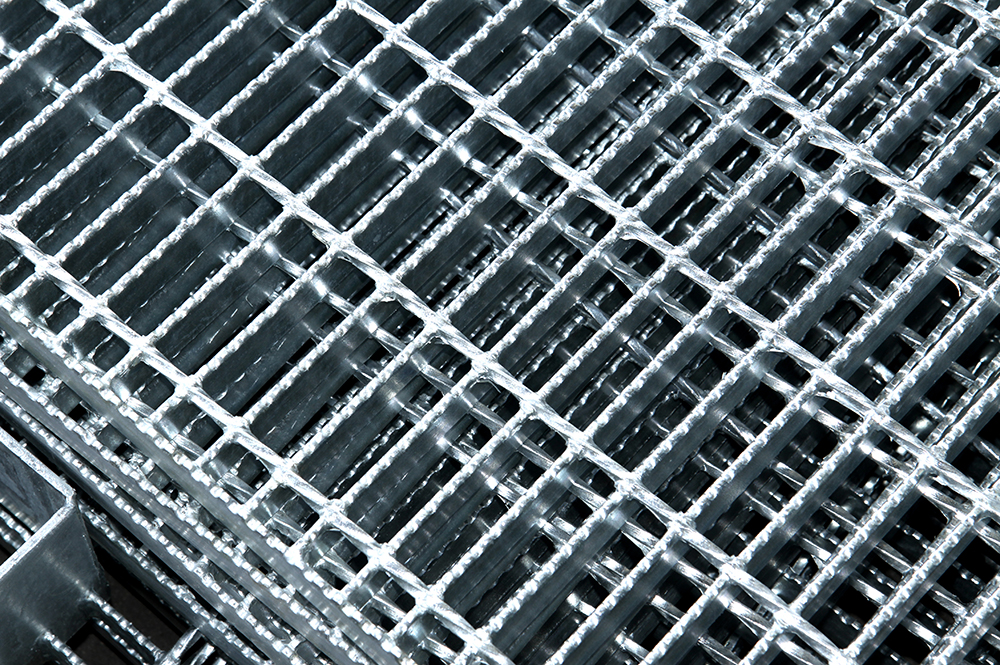